By Pat Burke, outgoing chairman, RPM Engineering Group.
Four years after final completion, RPM Consulting Engineers has taken the opportunity to review their most noteworthy project to date.
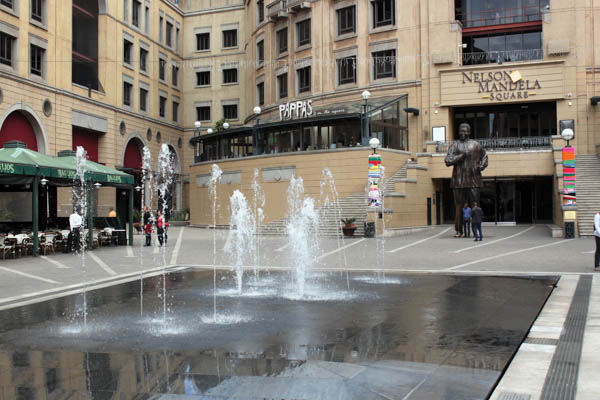
Nelson Mandela Square. Photo by Anagoria via Wikimedia Commons
Their observations concur that a project unencumbered by unrealistic budget restraints, together with a client possessing the appetite for an efficient, high quality and long-term solution, will produce an end result worthy of respect and appropriate acclaim.
In the heart of the Sandton CBD lies the iconic Nelson Mandela Square precinct, a mixed office, retail and entertainment destination.
IT ALWAYS SEEMS IMPOSSIBLE UNTIL IT’S DONE. – Nelson Mandela
Developed in the early 1990s, the original HVAC system comprised a conventional water-cooled direct expansion R22 design consisting of some (62 OFF) floor-standing, self-contained ducted packaged units located in plantrooms throughout the building. Close circuit cooling towers (11 OFF) at roof level, provided the means of heat rejection.
After some 24 years of operation and several successful attempts at extending the life of the equipment, the air-conditioning plant was eventually deemed no longer economically viable to retain. This decision was further influenced by the need for energy conservation as well as environmental considerations.
Following an extensive feasibility study which included in-depth site surveys, equipment selection and a small proto-type chilled water installation, a presentation to the owners was conducted on 26 August 2016.
The proposal was duly agreed upon and the services of RPM Consulting Engineers appointed accordingly. Design commenced in earnest, the contract documentation and drawings being issued to the relevant contractors at a pre-tender meeting held on 19 June 2017.
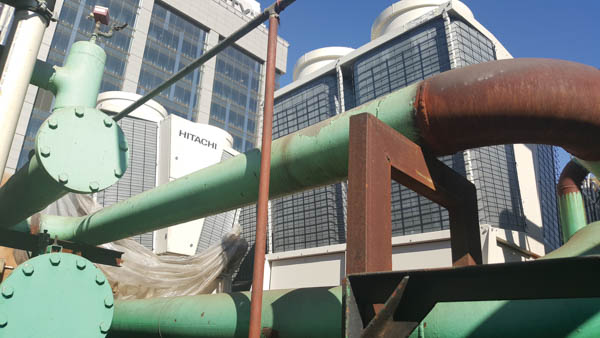
Existing condenser water pipe making way for new chiller modules. Image by RPM Consulting Engineers
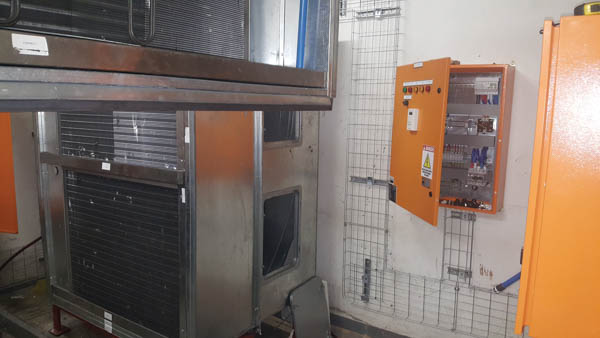
Bespoke CHW air-handling units being installed within existing plantrooms.. Image credit: RPM Consulting Engineers
Design and installation
It was subsequently agreed that the original water-cooled packaged unit arrangement would be replaced with a chilled water system. Air-cooled chilled water generators located within the existing cooling tower plantrooms at high level, would provide the necessary cooling to (62 OFF) bespoke chilled water air handling units. The units would be housed in the existing packaged-unit plantrooms located on the floors throughout the building.
Control would be by way of the upgrading and re-programming of the existing Building Management System (BMS).
Challenges presented
The decision to change the HVAC design came with its own set of challenges. These included power supply limitations, tenant considerations, plantroom space restrictions, chilled water pipe routes, change-over co-ordination, logistical planning, noise considerations and last, but no means least, no disruption to the air-conditioning of the building for the duration of the project. The engineers were under no illusion as to the difficulty of the task at hand.
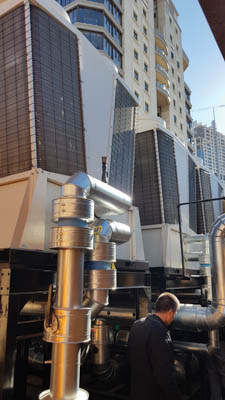
Equipment Selection
Chillers
The (4 OFF) 10m x 10m high level plantrooms available (to locate the chillers) necessitated the use of modular-type chillers. This need was further dictated by the fact that the old cooling towers required to be retained in this space to always enable ongoing air conditioning to the building.
The search was on for chillers of suitable modular capacity and dimensions best suited for the purpose. These were sourced from Hitachi Spain following a visit to a similar (albeit new) project in Camden, London, UK (28 OFF) 160kWr (nominal capacity) modular chillers were selected and duly ordered on 16 March 2017.
Existing cooling towers making way for air-cooled chillers at roof level. Image credit: RPM Consulting Engineers
Air handling units
The removal of the existing water-cooled DX packaged units from their individual plantrooms proved a straightforward but time-consuming exercise. Valve off, disconnect, cut up and remove from site.
Installing new chilled water air handling units into each existing plantroom proved a completely different prospect.
Access to the vast majority of plantrooms was by way of a 600 x 600 opening. This opening could not be enlarged due to the construction of the building (350mm thickness cast concrete walls). To overcome this obstacle, the air handling units were manufactured in various sections, suitably dimensioned to be accessed through the available openings.
Designed by RPM and manufactured locally, these air handling unit sections, including frames, panels, EC plug fans, chilled water coils, were suitably constructed for assembly within the plantroom. Manufactured from aluminium and stainless steel in only three physical sizes, uniformity and longevity is assured.
Controls
The control of the new plant consisted of the upgrade to the existing BMS to include additional functions. These new control functions are typically included for additional BMS controllers, sensors, LCD display units, pressure switches, over-heat thermostats, CO2 sensors, actuators, CHW control valves, CHW energy meters, power meters, master control panels and variable speed drives.
New chilled water pipe work nearing completion at roof level. Image credit: RPM Consulting Engineers
Typical CHW supply and return to each module. Image credit: RPM Consulting Engineers
Electrical
The electrical power supply was extended to the new chiller plantroom areas (4 OFF) at high level. This included for cable, control panels, control wiring, power meters with CT’s, new DB board chassis, temporary cooling tower connections, chiller and pump wiring, new chiller panels, cable termination, stripping out old wiring, testing, and commissioning.
Modular air-cooled chillers on completion.. Image credit: RPM Consulting Engineers
Following a successful tender process, the project commenced on 27 September 2017 with the site kick-off meeting.
A plan was duly formulated to always ensure ongoing plant operation (as required by the tenants) and to keep subsequent disruptions to an absolute minimum (weekends, after hours).
The same applied to the noise situation when breaking out and core drilling).
This was largely adhered to, with relatively few complaints from the tenants. Tenants were kept advised of looming disruptions by Centre Management, and thus made the necessary arrangements as applicable. Core drilling, being the noisiest discipline, was carried out after hours.
The inevitable ‘accident’ occurred, resulting in some flooding of office areas. New ceiling tiles and carpeting sufficed in keeping tenant claims to a minimum.
Theft of cable and equipment was a constant occurrence, with doors and padlocks being broken at random. Clearly insurance cover is essential on any site in today’s crime-ridden environment.
October and November 2017 saw the delivery of the (28 OFF) chillers. The delivery of the air handling units was processed in batches and assembled in the relevant plantrooms as required in terms of the planned programme, to include the chilled water pipework, electrical and controls.
The moving of the existing cooling towers to make way for the chillers took place from 14 December 2017 to 3 February 2018.
New CHW pumps being installed at roof level below chiller modules. Image credit RPM Consulting Engineers
Chiller installation nearing completion. Image credit: RPM Consulting Engineers
The main chiller rig took place over the weekend, 9-11 February 2018, an uninterrupted period of 38 hours.
With the chillers rigged into place, work commenced with the chilled water pipework, pumps, and electrical supply at roof level. So as not to disrupt the entire building, the project was planned in four segments, each being a tower riser. As the chiller modules were put into operation, so were the air handling units installed in the place of the existing water-cooled packaged units, plantroom for plantroom. In this way, several plantroom change-overs were completed during each weekend shut-down (Friday midday to 06h00 Monday) with the smooth transition to a chilled water system and relatively little tenant disruption.
The original fresh air system was re-utilised and upgraded to include variable speed drives, motorised dampers, and CO2 sensors throughout, to provide optimum energy savings. A night flushing programme was introduced to further enhance indoor conditions. Furthermore, when outside conditions dictate, controlled fresh air is introduced to the building for cooling purposes as and when necessary. This function forms part of the overall BMS control philosophy.
New electrical panel. Image credit: RPM Consulting Engineers
Pumps and pipe work being installed immediately below the chiller modules. Image credit: RPM Consulting Engineers
Green design
Not being a priority in the day, the original 1994 HVAC design did not take into account green design principals. In assessing the new design options, close consideration was applied to this aspect. What became clear was the need to reduce water and electrical consumption.
The design of the new chilled water plant was able to adequately address both the energy as well as the environmental impact requirements to the extent that substantial savings were possible. Addressing the water consumption was fairly straightforward, with the use of air-cooled chillers. The energy side was more of a concern as this required locating the most efficient chillers (in a modular form), each with sufficient capacity to render the project feasible from a cost and space perspective. This selection involved the COP, EER and SEER ratings for each relevant manufacturer.
Sound levels were a further important consideration, as the relevant chiller plantrooms are located immediately above residential apartments.
Initial cost comparisons (existing vs now) identified a conservative saving of R4.9 million an annum in respect of electrical and water consumption, as well as operational (Opex) costs, allowing for a 10.5-year payback period (2017 tariffs). To date, savings in excess of this are currently reported by way of the BMS.
Conclusion
Practical completion of the entire project was achieved on 30 June 2019, 24 months after the appointment of the successful contractor.
A project of this size, with all its logistical challenges, can only be achieved with careful planning, a good contractor and skilled project management. The project is now in its fourth year of operation and looking forward to serving the precinct for a further 20 years.
Article: RACA